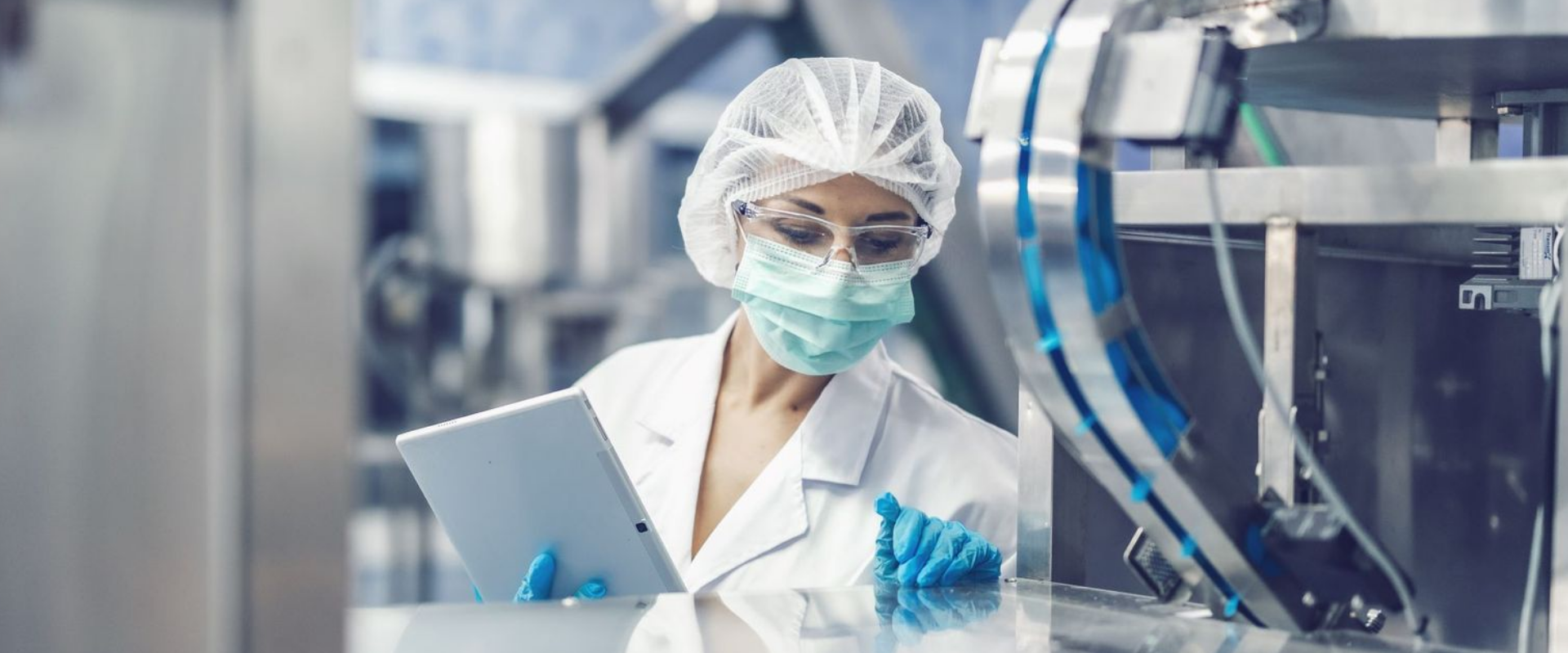
Supply chain resilience is a critical challenge in the life sciences industry, where manufacturing disruptions can take years to resolve and directly impact patient care. The complexity of regulatory compliance, combined with long lead times for scaling production, makes proactive planning and risk management essential.
Success requires deep operational expertise to build resilient supply chains that can consistently deliver critical treatments to patients. A pharmaceutical company engaged L.E.K. Consulting’s Operations and Supply Chain team to help address these challenges.
Tackling the resilience challenge
While all pharmaceutical companies must navigate complex manufacturing and regulatory requirements, the company’s siloed structure — managing drug substance, product and packaging independently — further complicated its situation.
As pharmaceutical pipelines grow more complex, with increasingly specialized treatments and global regulatory requirements, managing supply chains will only become more challenging. Rising costs and shifting market dynamics further underscore the need for proactive resilience strategies. For this company, several structural constraints made it even more difficult to build the necessary resilience into its supply chain:
- Manufacturing complexity: Contract development and manufacturing organizations impose high minimum orders and limited production flexibility.
- Qualification time: Adding production lines or suppliers requires 12-18 months of validation.
- Inventory costs: Safety stock for specialized products can reach tens of thousands of dollars per unit.
- Regulatory burden: Process or facility changes need extensive documentation and approval.
L.E.K.’s approach began with forming cross-functional teams for each product, conducting baseline assessments to align understanding as well as training teams on how changes affect upstream and downstream operations.
Mapping and modeling the supply chain
Detailed supply chain mapping revealed hidden vulnerabilities in the company’s siloed operations. Working backward from finished goods, the L.E.K. team created a digital representation showing how demand translated into capacity requirements.
This process uncovered critical constraints — some active pharmaceutical ingredient (API) production suites could only produce certain country-specific SKUs, while certain sterile fill-finish lines were restricted to specific API materials. These limitations showed how overlooked details could compromise resilience during disruptions.
During the engagement, a major disruption at a critical facility provided a real-world test of the supply chain’s resilience. The event threatened to halt production of multiple products, demonstrating how a single point of failure could quickly cascade throughout the network.
This concrete example helped reinforce executive buy-in for implementing more robust contingency measures and extended coverage across the portfolio (see Figure 1).
After mapping and verifying the supply chain — including parameters such as batch size, frequency, storage requirements, shelf life and bill of materials — the team built an end-to-end network model using a digital twin. This model replicated complex supply chain interactions over time, allowing L.E.K. to dynamically measure how inventory levels (both work-in-progress and finished goods) responded to shifting demand and potential disruptions.
The analysis revealed several critical vulnerabilities:
- Single-source dependencies: Key components relied on suppliers without scalable capacity.
- Site concentration: Redundant capacity often existed within single facilities, creating sitewide risks.
- Overlapping redundancies: Backup production lines serving multiple products created bottlenecks.
- Packaging vulnerabilities: Single-source bulk packaging threatened country-specific SKUs.
- Warehouse risks: Single storage sites created upstream production failure points.
- Limited contingency plans: Most products lacked emergency plans for alternative production.
- Demonstrated capacity gaps: Capacity levels used in production planning were overstated and did not represent the proven output, accounting for production inefficiencies and bottlenecks.
Turning insights into action
Resilience planning often feels nebulous, with generic solutions such as adding backup plans that fail to provide the specificity executives need. As well as investing in modular equipment, the L.E.K. team implemented other specific solutions across different product lines:
- Diversified suppliers: One product team established dual sourcing for critical components.
- Expanded redundancy: Another team invested in a mobile production lab, adding six months of buffer capacity.
- Created an inventory strategy: Targeted strategies brought inventory coverage from partial to full.
- Accepted strategic risk: Teams accepted certain risks where mitigation costs outweighed potential benefits.
The team approached investment decisions by prioritizing the value of protection over the likelihood of disruption. For example, when evaluating a $3 million investment to protect a $20 million revenue drug, the emphasis on ensuring patients never missed a dose justified the cost, underscoring the critical human impact behind the decision.
Delivering impact
The executive team gained clarity and confidence in understanding trade-offs and implementing solutions. During the engagement, the client made structural improvements that allowed the company to take immediate action, such as increasing the months of coverage for its average product, which provided critical breathing room to address disruptions. These early improvements laid the groundwork for implementing key longer-term strategies developed during the engagement:
- Implementing backup production lines and enhanced inventory strategies for high-priority products
- Launching supplier diversification initiatives to minimize single-source vulnerabilities
- Improving network resilience for proactive disruption management
Beyond these immediate actions, the client now has an advanced supply chain resilience model that enables ongoing scenario planning and risk management, ensuring the company can proactively adapt to future challenges. This approach not only protected critical operations and ensured continuous patient access to lifesaving therapies but also created a foundation for long-term supply chain resilience.
L.E.K.’s expertise in pharmaceutical and life sciences supply chains enables clients to achieve:
- Reduced supply chain disruption risk
- Decreased critical drug shortages
- Optimized network costs
- Enhanced supply flexibility
- Accelerated time to market for therapies
- Sustainable competitive advantages through operational excellence
To learn how L.E.K. can help build resilience in your supply chain and protect your ability to deliver critical therapies to patients, contact us today.
L.E.K. Consulting is a registered trademark of L.E.K. Consulting. All other products and brands mentioned in this document are properties of their respective owners. © 2025 L.E.K. Consulting
05282025100532